You might not realize that Elon Musk’s philosophical approach to problem-solving, known as first principles thinking, has been a critical driver of Tesla’s revolutionary manufacturing strategies. By systematically breaking down complex challenges into fundamental elements, Tesla’s engineering teams have reimagined electric vehicle production from its core components. Their unconventional methodology challenges traditional automotive assumptions, promising radical innovations that could reshape industrial manufacturing. Want to understand how this approach transforms industries from the ground up?
Key Takeaways
- Tesla deconstructs complex manufacturing challenges by breaking down battery production to fundamental material and design components, reducing production costs through meticulous raw material analysis.
- By vertically integrating battery production via Gigafactories, Tesla eliminates traditional supply chain inefficiencies and directly controls material sourcing, manufacturing, and technological innovation.
- The development of 4680 battery cells exemplifies first principles thinking, reimagining battery design from core material expenses to revolutionary structural and performance improvements.
- Tesla challenges industry assumptions by analyzing production processes at their most fundamental level, enabling radical cost reductions and technological breakthroughs in electric vehicle manufacturing.
- Strategic mining partnerships and in-house technology development allow Tesla to transform battery production economics, creating competitive advantages through systematic deconstruction of existing manufacturing paradigms.
The Battery Cost Challenge

When Tesla first entered the electric vehicle market, battery costs emerged as a formidable technological and economic barrier. The industry had accepted high prices as inevitable, but Tesla’s first principles thinking challenged this conventional wisdom. By deconstructing battery costs and analyzing raw materials, they discovered that material expenses could be dramatically reduced. Rather than accepting existing solutions, they approached the challenge from scratch, identifying that raw material costs were markedly lower than market prices.
This analytical approach revealed that traditional supply chains were inefficient and overpriced. By reimagining battery production through vertical integration and direct material sourcing, Tesla transformed an apparently insurmountable obstacle into a strategic opportunity for innovation and cost reduction in electric vehicles.
Deconstructing Manufacturing Processes
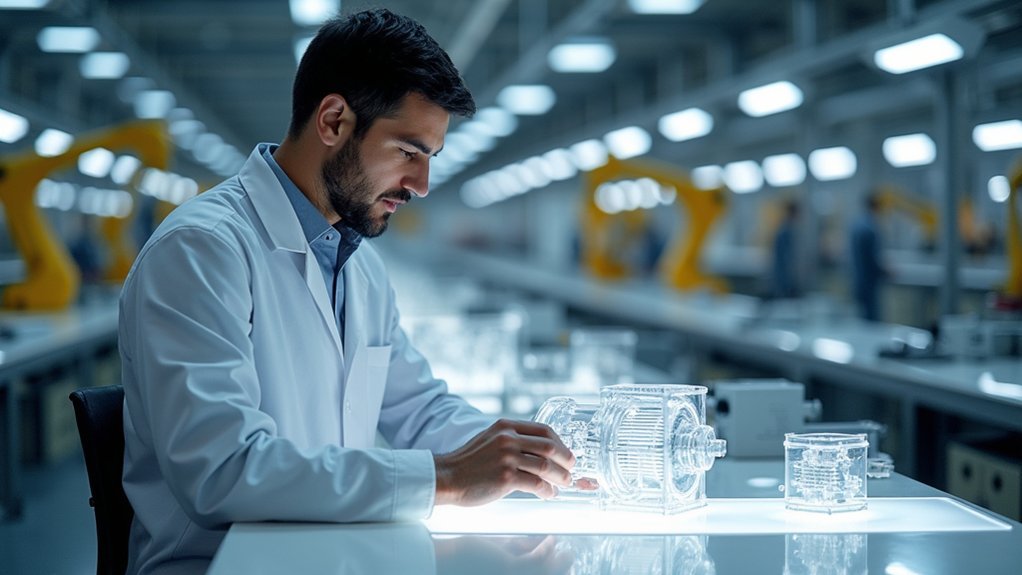
Building upon their breakthrough in battery cost reduction, Tesla’s manufacturing innovation extends far beyond material procurement. They’ve applied first principles to deconstructing manufacturing processes with remarkable precision:
Tesla’s manufacturing revolution transcends conventional boundaries, redefining industrial innovation through radical first-principles thinking.
- Vertical Integration: Constructing Gigafactories to eliminate external dependencies
- Battery Cell Redesign: Developing 4680 cells that fundamentally reimagine production capabilities
- Gigacasting Techniques: Simplifying assembly through radical structural redesigns
- Component Optimization: Breaking down production into fundamental elements for radical efficiency
Vertical Integration Strategy
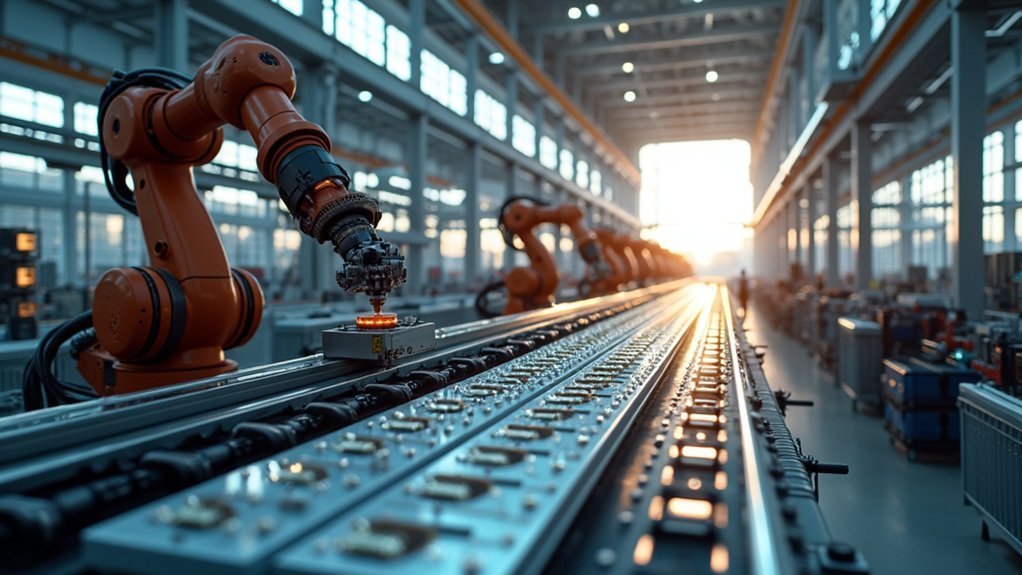
Because Tesla’s manufacturing revolution hinges on strategic control, the company’s vertical integration strategy represents a paradigm-shifting approach to automotive and energy production. By implementing First Principles Thinking, Tesla deconstructs fundamental truths about traditional manufacturing and rebuilds processes from the ground up. You’ll observe how they’ve eliminated supplier dependencies through direct mining partnerships and in-house battery production at Gigafactories. Applying First Principles Thinking enables Tesla to dramatically reduce production costs by controlling the entire supply chain—from raw material extraction to final vehicle assembly. This vertical integration strategy isn’t just about cost reduction; it’s a systematic approach to reimagining manufacturing efficiency. By scaling to six global Gigafactories and producing 200 GWh/year, Tesla demonstrates how radical rethinking can transform industrial paradigms.
Breakthrough Battery Technology

Through radical deconstruction of battery technology’s fundamental components, Tesla has engineered a transformative approach that challenges conventional manufacturing paradigms. By applying First Principles Thinking, they’ve solved critical battery production challenges through innovative strategies:
- Breaking down battery cell costs to raw material expenses
- Developing the revolutionary 4680 battery design
- Establishing direct mining partnerships to reduce material costs
- Creating vertical integration through Gigafactory production
You’ll recognize that solving problems at their most fundamental level allows Tesla to reimagine battery technology. Their breakthrough approach dismantles traditional constraints by analyzing each component’s intrinsic value. The company’s ability to apply First Principles Thinking has enabled them to dramatically reduce battery production costs, positioning themselves at the cutting edge of electric vehicle manufacturing. This methodical, analytical approach transforms seemingly insurmountable challenges into strategic opportunities for technological advancement.
Market Transformation Results

While Tesla’s first principles approach revolutionized battery technology, the market transformation results have been nothing short of paradigm-shifting. By systematically breaking down complex problems into fundamental solutions, Tesla reshaped the automotive landscape, compelling traditional manufacturers to accelerate electrification strategies.
Market Metric | Tesla Impact | Industry Response |
---|---|---|
EV Market Share | 65% (U.S.) | Rapid Adaptation |
Vehicle Production | 2M Annually | Scaling Investments |
Market Valuation | $1T+ | Competitive Pressure |
Technology Innovation | Disruptive | Strategic Pivoting |
Tesla’s first principles methodology demonstrated that innovative thinking could dramatically transform markets. Their approach challenged industry assumptions, proving that radical solutions emerge when you deconstruct conventional wisdom. By focusing on fundamental physics and engineering principles, Tesla didn’t just improve electric vehicles—they redefined what’s possible in automotive technology and market dynamics.
Frequently Asked Questions
What Is the First Principles Thinking of Elon Musk?
You’ll use first principles thinking to deconstruct complex problems, break them down to fundamental truths, and solve challenges through innovative strategies that challenge conventional wisdom by applying critical, analytical reasoning.
What Is Tesla’s First Principles Approach?
You’ll break down complex challenges like a tech surgeon, dissecting automotive engineering to its core. Tesla’s first principles approach revolutionizes problem-solving by questioning assumptions, innovating design, and radically reimagining manufacturing through fundamental engineering principles.
What Type of Thinking Does Elon Musk Use?
You’ll discover Elon Musk’s mindset centers on first principles thinking: breaking complex problems into fundamental truths, enabling innovative problem solving that challenges conventional wisdom and drives disruptive technology through strategic, analytical cognitive frameworks.
What Management Theory Does Tesla Use?
You’ll see Tesla’s revolutionary management theory in action through first principles thinking, where they deconstruct complex problems, prioritize radical innovation, and make decisions by questioning conventional wisdom to drive transformative technological advancements.
Conclusion
You’ve witnessed how Tesla’s first principles approach dismantled automotive industry orthodoxies. By questioning every fundamental assumption, they transformed electric vehicle manufacturing from an expensive niche to a scalable revolution. Remember: “Necessity is the mother of invention.” Tesla didn’t just redesign cars; they reimagined an entire technological ecosystem, proving that radical innovation emerges when you deconstruct complex problems to their most basic elements and rebuild with strategic, scientific precision.